Cooling e-charging station components and battery storage system
EKL heat sinks for charging stations and storage systems
Intelligent energy: the symbiosis of e-charging stations and solar battery storage systems
E-charging stations for electric vehicles and solar battery storage in buildings have some special technical features. An e-charging station usually offers different charging modes to fulfil different customer needs when charging, such as normal charging and fast charging. Communication between the vehicle and charging station must also be compatible with the wallbox at home, which is often made possible by a Combined Charging System (CCS).
Battery storage systems, on the other hand, are characterised by product features such as capacity, service life, efficiency and size. They are an essential part of the energy infrastructure in modern homes as they can provide stored energy from renewable sources such as solar panels. Electronic components in this environment that require cooling include rectifiers, inverters, processors, power converters and the batteries themselves.
Battery storage systems, on the other hand, are characterised by product features such as capacity, service life, efficiency and size. They are an essential part of the energy infrastructure in modern homes as they can provide stored energy from renewable sources such as solar panels. Electronic components in this environment that require cooling include rectifiers, inverters, processors, power converters and the batteries themselves.
Customised EKL cooling technology for optimised performance of your charging infrastructure
Effective thermal management is crucial for e-charging stations, wallboxes and battery storage systems in order to ensure the service life and reliability of these components. Heat sink solutions from EKL ensure that heat loss is efficiently dissipated into the environment. They ensure the ideal operating temperature of your charging stations, charging plugs or battery management systems (BMS) and protect the electronic components and peripherals from damage by overheating.
Your heat sink manufacturer for components in e-charging stations, charging plugs and BMS
EKL has been the development partner and supplier for customised and cost-optimised cooling solutions for 30 years. With our proven cooling technologies, we prevent your device from getting too hot and can make a decisive contribution to the performance and reliability of your e-charging stations and BMS (battery management systems).
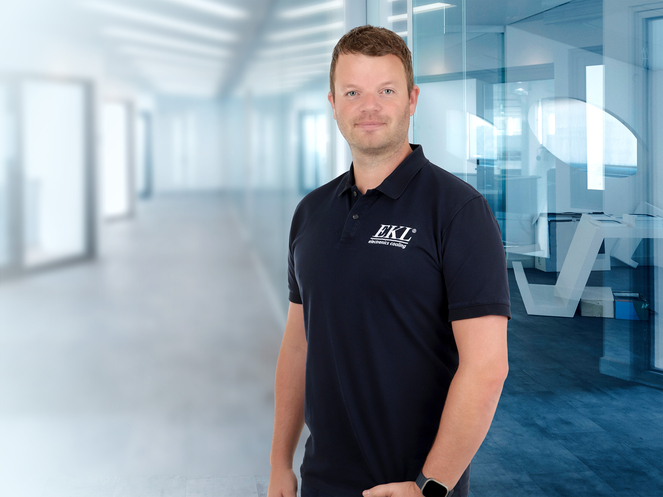
Let's talk about your cooling task!
Thomas Würzer
Sales Department
+49 (0)7561 9837-44
t.wuerzer@ekl-ag.de
Make an appointment Enquiries by e-mail
Thomas Würzer
Sales Department
+49 (0)7561 9837-44
t.wuerzer@ekl-ag.de
Make an appointment Enquiries by e-mail
CB-Scheme certified fans for maximum safety EKL relies on tested quality
Components that meet globally recognised safety standards are required for use in international markets. Fans with IECEE CB Scheme certification fulfil precisely these requirements - tested in accordance with standards such as IEC 62368-1 and approved for global use.
EKL AG supplies or installs CB-certified fans in its high-performance heat sink solutions on request, e.g. for charging stations and battery storage systems. Customers benefit from:
EKL AG supplies or installs CB-certified fans in its high-performance heat sink solutions on request, e.g. for charging stations and battery storage systems. Customers benefit from:
- Safety-tested components in accordance with international IEC standards
- Reliable documentation and traceability
- Highest quality assurance through EKL test procedures
- Fast market approval in over 50 countries
Typical applications for EKL heat sinks in e-mobility and electricity storage
In electronics, the heat generated by current-carrying components is an unavoidable and usually annoying side effect. As a product manager and development engineer of electronic systems, free yourself from the risk of overheating and expensive development loops by placing the thermal management of your device in the hands of EKL! We see ourselves as a partner in your development, pursuing the same goals as you: to manufacture a reliable, high-quality and durable product at competitive prices.
Cooling charging stations for electric vehicles
Public charging stations for electric vehicles are complex systems. These include power electronics, control units and safety mechanisms that monitor and regulate the charging process. The power electronics in particular, which are responsible for converting and controlling the flow of electricity, generate a lot of heat. These power transistors and thyristors therefore require efficient cooling in order to ensure safe and optimal "refuelling". EKL develops and produces cooling systems specially designed for these applications. Our product range extends from air-cooled high-performance heat sinks to liquid cooling to dissipate the heat generated and maintain the performance of the charging station even at high ambient temperatures.
Cooling wallbox for electric cars
One of the key components of a wallbox for charging electric cars is phase current detection, which ensures that none of the three current phases is overloaded. The Electric Vehicle Charge Controller (EVCC), which controls the communication between the vehicle and the EV wallbox, monitors the charging process. Some of these components, especially those connected to the power electronics, require cooling. Heat sinks from EKL prevent overheating in the wallbox for electric cars, ensure consistent efficiency in the charging process and extend the service life of your wallbox product.
Cooling battery management systems (BMS) for solar batteries
Batteries are essential for storing electricity in electric cars and buildings - and they are expensive. Battery management systems (BMS) are the centrepiece of modern battery technology, as they protect the investment in battery storage systems by ensuring constant performance, safety and a long service life. Sensors collect data on voltage, current and temperature to ensure optimal battery performance. Switches play a critical role by making or breaking the connection between the battery, load and charger. Microcontrollers process the collected data and execute complex algorithms to control and monitor the battery. This also includes preconditioning, i.e. cooling or heating the solar storage tanks to the ideal charging temperature. Communication modules transmit the collected data to other systems. Displays provide users with important information about the battery status.
Power switches and converters in particular, which switch high currents and adjust voltages, generate significant power losses. Power semiconductors such as transistors and diodes used in these components are particularly susceptible to overheating.
Heat sinks, fans or liquid cooling systems from EKL are an integral part of a BMS to ensure a stable operating temperature and ensure the longevity and reliability of the battery.
Power switches and converters in particular, which switch high currents and adjust voltages, generate significant power losses. Power semiconductors such as transistors and diodes used in these components are particularly susceptible to overheating.
Heat sinks, fans or liquid cooling systems from EKL are an integral part of a BMS to ensure a stable operating temperature and ensure the longevity and reliability of the battery.
Cooling electric car charging plugs
Charging plugs such as the type 2 for electric cars have the task of converting the alternating current from the power grid into direct current via an integrated rectifier, which is then stored in the vehicle's high-voltage battery. These components must be cooled during the charging process, especially the power electronics of the AC/DC converter. For the charging control of electric vehicles at household sockets, the in-cable control box performs safety and communication functions so as not to overload the household socket. The high currents generate heat in the electronic components. EKL offers thermal management using heat sinks to protect your components from overheating even at peak loads.
High-performance heat sinks for refuelling and storing electricity
EKL - Everything from a single source
The temperature of electronic components must remain within the tolerated range, as excessive heating can shorten their service life and impair their performance. EKL provides you with expert support in solving these heat problems efficiently and economically using passive heat sinks, fans, heat pipes, liquid heat sinks or other thermal management technologies.
EKL is therefore your perfect solution partner for cost-optimised temperature regulation of all components in your electronic device. We are at your side in every project phase, from the initial idea, design and prototype construction through to series production - and beyond!
The temperature of electronic components must remain within the tolerated range, as excessive heating can shorten their service life and impair their performance. EKL provides you with expert support in solving these heat problems efficiently and economically using passive heat sinks, fans, heat pipes, liquid heat sinks or other thermal management technologies.
EKL is therefore your perfect solution partner for cost-optimised temperature regulation of all components in your electronic device. We are at your side in every project phase, from the initial idea, design and prototype construction through to series production - and beyond!
Personal point of contact
From the initial project phase to the delivery of your customised cooling technology, you will always have a personal point of contact at EKL We are always available to provide you with competent and responsive support.
Full service from the idea to logistics
Concentrate your core competence on product development. We offer all project services relating to cooling - from the initial consultation, idea development and thermal simulation, prototype construction and optimisation, through to punctual delivery and reliable logistics and warehousing.
Variety of manufacturing technologies
We are one of the heat sink manufacturers with the widest range of manufacturing technologies. This enables us to offer a service portfolio that is designed for the development and production of your truly best cooling solution - at an excellent price-performance ratio.
Performance optimisation + cost optimisation
EKL actively supports you in reducing your manufacturing costs without compromising quality or performance. Product cost reduction is an important aspect that we achieve for you through efficient design, careful material selection and reliable manufacturing partners.
Pre-assembled assemblies + packaging
We actively assist your production staff by supplying pre-assembled assemblies. This not only reduces your labour costs per device, but also guarantees the highest quality. Your sensitive heat sinks or assemblies are protected for transport using customised packaging.
Warehouse and logistics in Germany
With over 1100 pallet spaces, we offer tailor-made logistics solutions and minimise your storage costs through stockpiling and consignment stock, just-in-time deliveries, coordinated delivery schedules and flexible shipping options for individual requirements.
The EKL project stages for your cooling solutionChoose your point of entry!
Our offer is as flexible as your needs. Are you still early in the development phase and want an idea generator for the best cooling solution? Do you have a ready-made device that gets too hot? Or are you simply looking for an alternative or additional supplier for a heat sink already used in series production? In EKL you will always find a flexible, agile and responsible partner for the cooling of your electronic components and complete systems, whatever the project phase. We look forward to your enquiry!
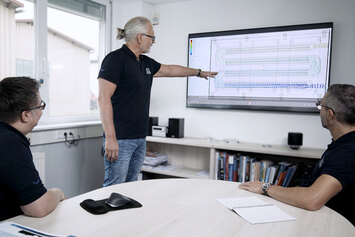
Counselling
Concept
Concept
In personal contact and open dialogue with you, our engineers create the creative space and framework to design the best cooling solution for your requirements from the wealth of options available.
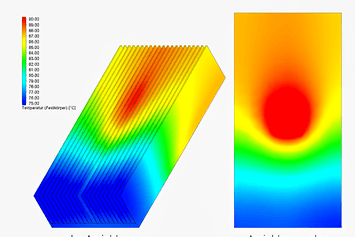
Development
Feasibility / simulation
Feasibility / simulation
We test the idea for your heat sink virtually in the thermal simulation. Realistic computer simulations allow variations in manufacturing processes, system structures and other parameters.

Performance optimisation
Even a well-functioning heat sink can still be optimised. We determine the "how" and "how much" by simulating different materials or cooling technologies, for example, as well as simulating various environmental parameters.
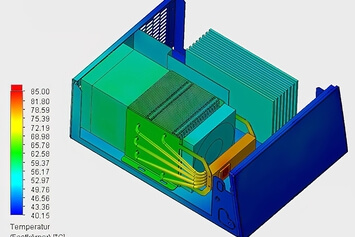
Cost optimisation
An expensive heat sink can often be made significantly cheaper by using an alternative manufacturing process. Whether with the same or application-specific performance: we support your product development in reducing costs.
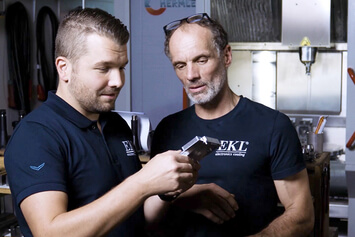
Production drawing
Prototype construction
Prototype construction
Prototypes from our design department enable early testing and targeted solutions to problems in your device. We create your functional and design prototypes with our in-house CNC production.
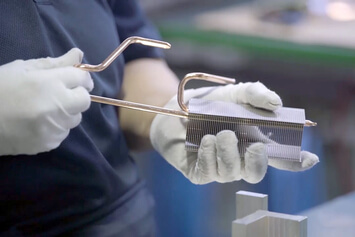
Series production
small to large
small to large
By manufacturing in-house and in Asia, we can offer all types of heat sinks from small to large series at competitive unit prices. We impress our long-standing customers with our consistently high quality.
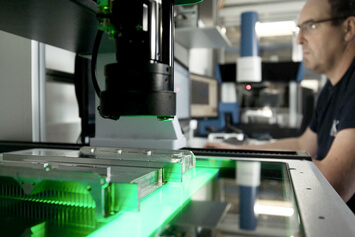
Sampling
Incoming goods inspection
Incoming goods inspection
We make no compromises when it comes to quality: Development takes place in Germany and all series products are analysed by our German test laboratory according to test plans using state-of-the-art methods.
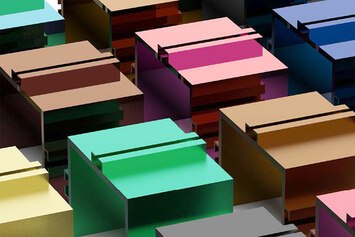
Surface finishing
Anodising, powder coating, painting etc. protect your heat sinks from corrosion and environmental influences. But colour is not just chic, because dark-coloured heat sinks also emit more radiant heat.
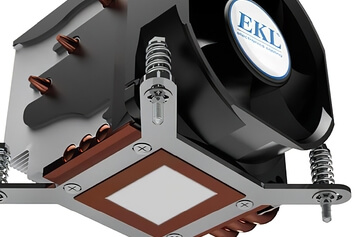
Assemblies
Pre-assembly
Pre-assembly
We actively relieve your production with pre-assembled assemblies. This reduces your workload per device and guarantees the highest quality, because as cooling professionals we ensure that the heat sink is optimally attached.
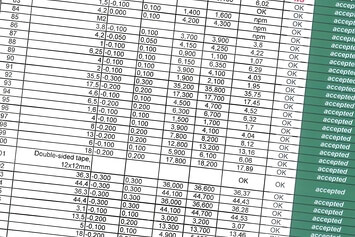
Quality assurance
Test plans
Test plans
We test according to our own and customer-specific test plans using the latest rapid thermal measuring equipment, 3D measuring machines, assembly tests and testing of various application scenarios.
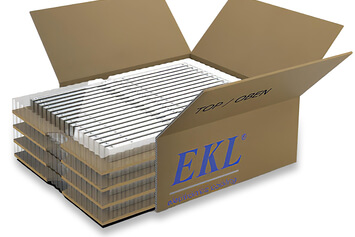
Packaging design
Packaging production
Packaging production
EKL develops and produces customised packaging to optimally protect your sensitive heat sinks or assemblies in the sometimes harsh transport and storage environments.
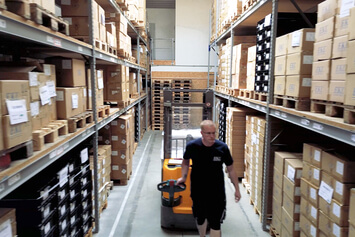
Warehouse
& Logistics
& Logistics
With large storage capacities, we offer production-related stocking and consignment warehouses, just-in-time deliveries, customised delivery schedules and flexible shipping options for your individual requirements.
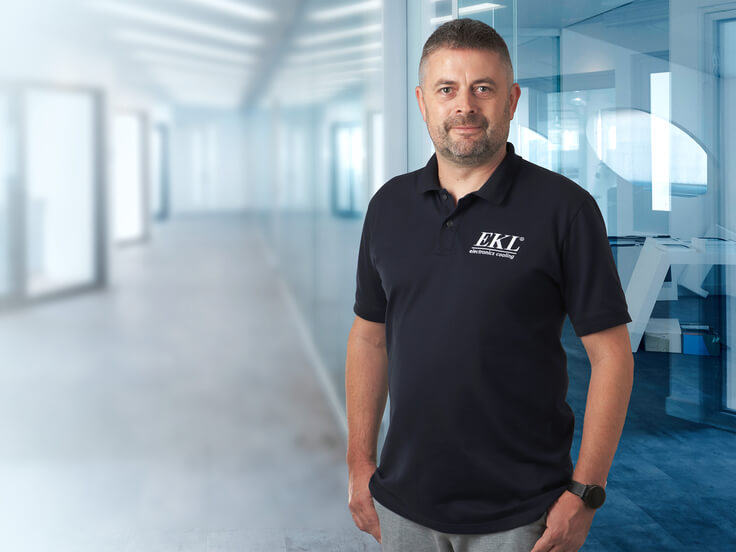
Let's talk about your cooling task!
Frank Sichler
Sales Manager
+49 (0)7561 9837-47
f.sichler@ekl-ag.de
Make an appointment Enquiries by e-mail
Frank Sichler
Sales Manager
+49 (0)7561 9837-47
f.sichler@ekl-ag.de
Make an appointment Enquiries by e-mail