Liquid cooled heat sink for electronics with high heat generation
Skilful heat management with liquid coolers
Liquid heat sinks are an efficient solution for heat dissipation in electronic systems where conventional passive heat sinks or coolers with fans reach their limits. They are mainly used to cool high-performance processors, which can generate a large amount of heat in a small space. These cooling systems utilise liquids such as water, glycol or oil, which flow through recessed pipes or specially designed channels within the heat sinks. This effectively transports the heat to a desired location - away from the heat source.
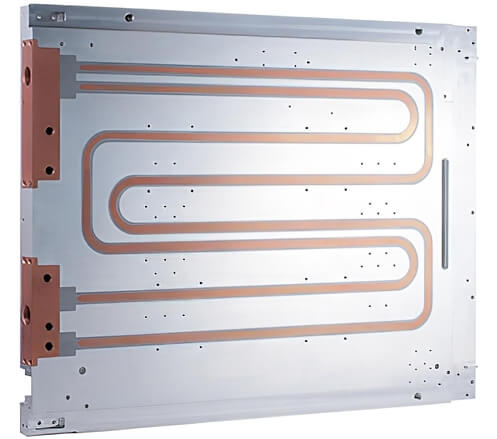
Advantages of liquid cooling
- Efficient and compact heat dissipation: Liquid heat sinks enable space-saving, fast and efficient heat dissipation from electronic components, which is essential for their reliable function.
- Reliable protection against overheating and power loss: Liquid heat sinks are particularly effective in cooling components that can reach very high operating temperatures. It is easy to route the coolant to another location, e.g. by connecting it to an existing external cooling circuit.
- Adaptability: They can be customised to different applications and available installation space to ensure optimised cooling performance.
- Versatility of materials: Various materials such as copper and aluminium, but also stainless steel, can be used to optimise heat dissipation depending on requirements and environmental influences. They can be designed as water heat sinks, but also with glycol or oil.
- High flexibility in production: EKL has various manufacturing technologies for liquid heat sinks, which are selected depending on the number of units, application requirements and cost aspects.
EKL: Your liquid heat sink manufacturer
The basis of an EKL liquid cooler usually consists of an aluminium cooling plate with embedded copper tubes. Liquid heat sinks are frequently used in electromobility, power electronics and precision sensor technology due to their high efficiency and ability to enable compact designs. You can rely on our more than 30 years of expertise in the development and production of electronic heat sinks. Reliable thermal management is a decisive factor for the success of your electronic product!
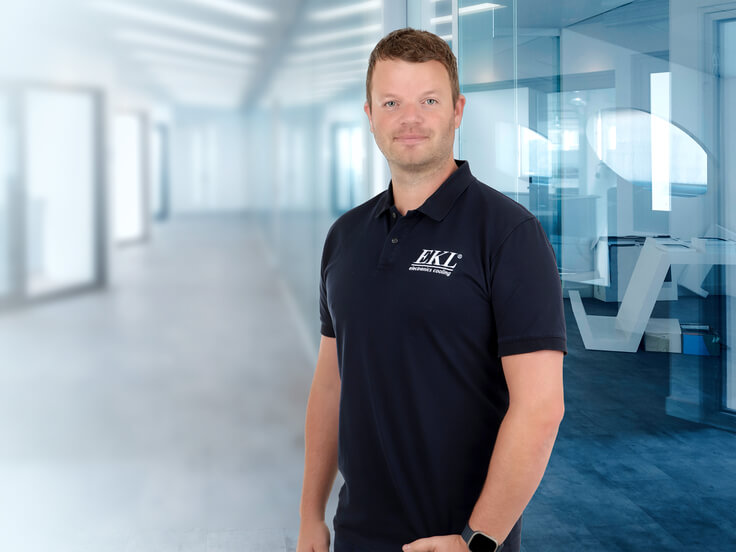
Let's talk about your cooling task!
Thomas Würzer
Sales Department
+49 (0)7561 9837-44
t.wuerzer@ekl-ag.de
Make an appointment Enquiries by e-mail
Thomas Würzer
Sales Department
+49 (0)7561 9837-44
t.wuerzer@ekl-ag.de
Make an appointment Enquiries by e-mail
Liquid cooling for high-performance electronics in the application
Applications that work with high power density components and require Liquid Cooled Heatsink Solutions for efficient heat dissipation are typical:
Battery management systems in electric vehicles and stationary storage, which are essential for monitoring and controlling battery performance.
In medical technology,liquid coolers provide reliable cooling for devices used in diagnostics and therapy.
In the renewable energy sector, water heat sinks contribute to the stability of solar inverters and wind turbines.
In railway technology,air-cooled liquid chillers play a role in the temperature regulation of traction converters.
In high-voltage inverters, which are used in power grids to adjust voltage and frequency levels, they cool the power electronics.
In laser technology , the laser beam sources, lenses and (in laser cutter applications) the laser cutting head must be kept within the temperature tolerance with liquid cooling in order to ensure optimum cutting quality and working speed.
In IT server farms, there area large number of high-performance computers in a confined space, whose waste heat is reliably and quickly transported to the outside by Liquid Heat Sink.
In medical technology,liquid coolers provide reliable cooling for devices used in diagnostics and therapy.
In the renewable energy sector, water heat sinks contribute to the stability of solar inverters and wind turbines.
In railway technology,air-cooled liquid chillers play a role in the temperature regulation of traction converters.
In high-voltage inverters, which are used in power grids to adjust voltage and frequency levels, they cool the power electronics.
In laser technology , the laser beam sources, lenses and (in laser cutter applications) the laser cutting head must be kept within the temperature tolerance with liquid cooling in order to ensure optimum cutting quality and working speed.
In IT server farms, there area large number of high-performance computers in a confined space, whose waste heat is reliably and quickly transported to the outside by Liquid Heat Sink.
This wide range of applications demonstrates the versatility and importance of liquid cooling in highly developed technological systems.
The right manufacturing technology for every application
Brazed liquid heat sinks
Heat sinks with soldered top and bottom sides are suitable for demanding applications. This enables the realisation of complex structures, such as integrated cooling fins. The cooling channels are produced by milling into the corresponding plates. Due to the specific manufacturing process, the maximum size of the heat sinks is limited. More about the soldering manufacturing process
Cold forged liquid heat sinksLiquid heat sinks using the cold extrusion process
Cold-forged heat sinks made of high-purity copper or aluminium offer efficient heat dissipation thanks to the integrated cooling fins on the surface of the element. The special manufacturing process ensures ideal heat transfer from the cooling plates via the cooling channels to the cooling fins. These heat sinks are frequently used in the temperature regulation of IGBT (Insulated-Gate Bipolar Transistor) components.
More about the cold forging manufacturing process
More about the cold forging manufacturing process
Friction stir welding of liquid heat sinks
Liquid heat sinks produced by friction welding do not require separate tubes, as their cooling channels are machined directly into the aluminium cold plate. These channels can also be drawn tighter, as no minimum bending radii need to be observed, as is the case with embedded copper tubes. Nevertheless, there are limitations in terms of shaping due to the less smooth inner surfaces of the channels. The production process using friction welding is suitable for the production of individual parts and prototypes as well as for mass production.
More about the friction stir welding manufacturing process
More about the friction stir welding manufacturing process
Liquid heat sinks from the extrusion process
The cost-effective series production of aluminium liquid heat sinks with drawn-in cooling channels is achieved by means of step-by-step extrusion. In this way, the internal cooling channel remains stable. The heat sink is then sealed at the ends with relevant additional parts or installed in the cooling system. The extrusion process is ideal for the production of complete series, thanks to relatively low tooling costs.
More about the extrusion manufacturing process
More about the extrusion manufacturing process
Die-cast aluminium liquid heat sinks
The aluminium die-casting process has established itself as a method for producing liquid cooling systems in large quantities. As only the cooling plate is produced using this process, there are no restrictions regarding the material of the cooling tubes. Depending on the application and the cooling liquid, tubes made of aluminium, copper or stainless steel can be inserted into the preformed grooves. Due to these properties, die-cast aluminium liquid coolers are widely used in electromobility, for example.
More about the friction stir welding manufacturing process
More about the friction stir welding manufacturing process
EKL - Everything from a single source
The temperature of electronic components must remain within the tolerated range, as excessive heating can shorten their service life and impair their performance. EKL provides you with expert support in solving these heat problems efficiently and economically using passive heat sinks, fans, heat pipes, liquid heat sinks or other thermal management technologies.
EKL is therefore your perfect solution partner for cost-optimised temperature regulation of all components in your electronic device. We are at your side in every project phase, from the initial idea, design and prototype construction through to series production - and beyond!
The temperature of electronic components must remain within the tolerated range, as excessive heating can shorten their service life and impair their performance. EKL provides you with expert support in solving these heat problems efficiently and economically using passive heat sinks, fans, heat pipes, liquid heat sinks or other thermal management technologies.
EKL is therefore your perfect solution partner for cost-optimised temperature regulation of all components in your electronic device. We are at your side in every project phase, from the initial idea, design and prototype construction through to series production - and beyond!
Personal point of contact
From the initial project phase to the delivery of your customised cooling technology, you will always have a personal point of contact at EKL We are always available to provide you with competent and responsive support.
Full service from the idea to logistics
Concentrate your core competence on product development. We offer all project services relating to cooling - from the initial consultation, idea development and thermal simulation, prototype construction and optimisation, through to punctual delivery and reliable logistics and warehousing.
Variety of manufacturing technologies
We are one of the heat sink manufacturers with the widest range of manufacturing technologies. This enables us to offer a service portfolio that is designed for the development and production of your truly best cooling solution - at an excellent price-performance ratio.
Performance optimisation + cost optimisation
EKL actively supports you in reducing your manufacturing costs without compromising quality or performance. Product cost reduction is an important aspect that we achieve for you through efficient design, careful material selection and reliable manufacturing partners.
Pre-assembled assemblies + packaging
We actively assist your production staff by supplying pre-assembled assemblies. This not only reduces your labour costs per device, but also guarantees the highest quality. Your sensitive heat sinks or assemblies are protected for transport using customised packaging.
Warehouse and logistics in Germany
With over 1100 pallet spaces, we offer tailor-made logistics solutions and minimise your storage costs through stockpiling and consignment stock, just-in-time deliveries, coordinated delivery schedules and flexible shipping options for individual requirements.
The EKL project stages for your cooling solutionChoose your point of entry!
Our offer is as flexible as your needs. Are you still early in the development phase and want an idea generator for the best cooling solution? Do you have a ready-made device that gets too hot? Or are you simply looking for an alternative or additional supplier for a heat sink already used in series production? In EKL you will always find a flexible, agile and responsible partner for the cooling of your electronic components and complete systems, whatever the project phase. We look forward to your enquiry!
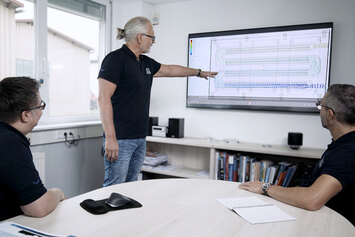
Counselling
Concept
Concept
In personal contact and open dialogue with you, our engineers create the creative space and framework to design the best cooling solution for your requirements from the wealth of options available.
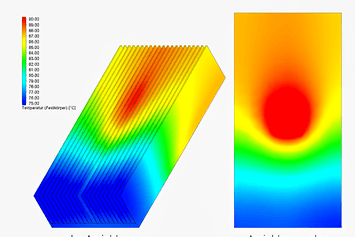
Development
Feasibility / simulation
Feasibility / simulation
We test the idea for your heat sink virtually in the thermal simulation. Realistic computer simulations allow variations in manufacturing processes, system structures and other parameters.

Performance optimisation
Even a well-functioning heat sink can still be optimised. We determine the "how" and "how much" by simulating different materials or cooling technologies, for example, as well as simulating various environmental parameters.
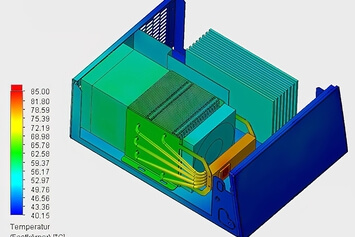
Cost optimisation
An expensive heat sink can often be made significantly cheaper by using an alternative manufacturing process. Whether with the same or application-specific performance: we support your product development in reducing costs.
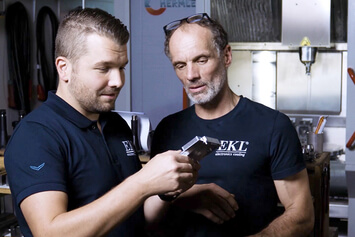
Production drawing
Prototype construction
Prototype construction
Prototypes from our design department enable early testing and targeted solutions to problems in your device. We create your functional and design prototypes with our in-house CNC production.
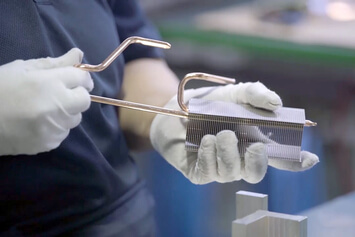
Series production
small to large
small to large
By manufacturing in-house and in Asia, we can offer all types of heat sinks from small to large series at competitive unit prices. We impress our long-standing customers with our consistently high quality.
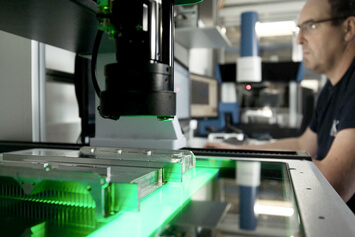
Sampling
Incoming goods inspection
Incoming goods inspection
We make no compromises when it comes to quality: Development takes place in Germany and all series products are analysed by our German test laboratory according to test plans using state-of-the-art methods.
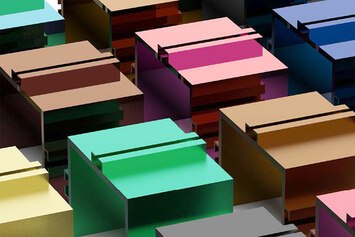
Surface finishing
Anodising, powder coating, painting etc. protect your heat sinks from corrosion and environmental influences. But colour is not just chic, because dark-coloured heat sinks also emit more radiant heat.
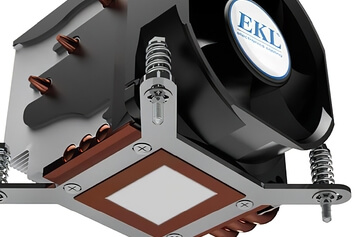
Assemblies
Pre-assembly
Pre-assembly
We actively relieve your production with pre-assembled assemblies. This reduces your workload per device and guarantees the highest quality, because as cooling professionals we ensure that the heat sink is optimally attached.
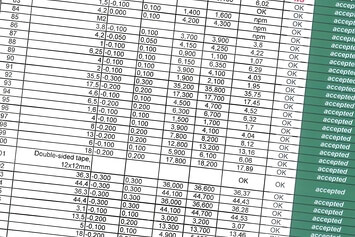
Quality assurance
Test plans
Test plans
We test according to our own and customer-specific test plans using the latest rapid thermal measuring equipment, 3D measuring machines, assembly tests and testing of various application scenarios.
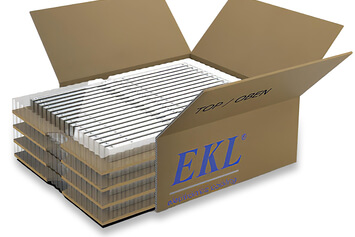
Packaging design
Packaging production
Packaging production
EKL develops and produces customised packaging to optimally protect your sensitive heat sinks or assemblies in the sometimes harsh transport and storage environments.
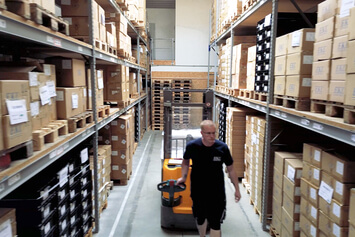
Warehouse
& Logistics
& Logistics
With large storage capacities, we offer production-related stocking and consignment warehouses, just-in-time deliveries, customised delivery schedules and flexible shipping options for your individual requirements.
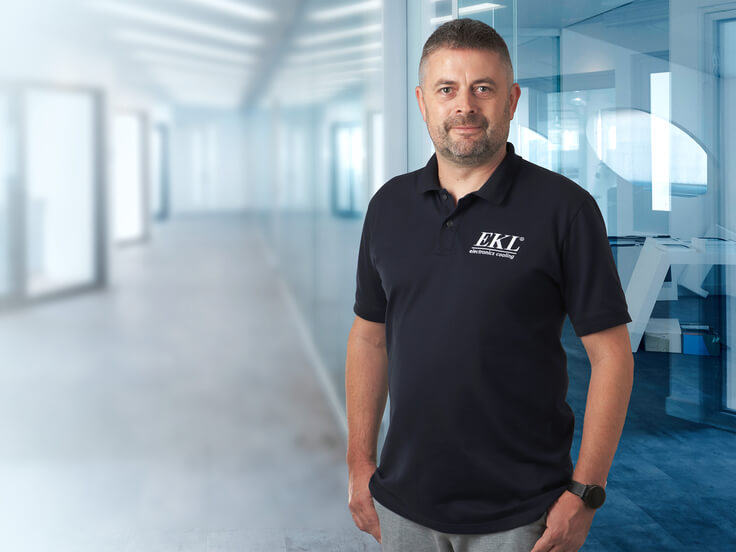
Let's talk about your cooling task!
Frank Sichler
Sales Manager
+49 (0)7561 9837-47
f.sichler@ekl-ag.de
Make an appointment Enquiries by e-mail
Frank Sichler
Sales Manager
+49 (0)7561 9837-47
f.sichler@ekl-ag.de
Make an appointment Enquiries by e-mail