Cooling electronics and inverters in PV and wind turbines
EKL heat sinks for renewable energies
From rectifiers for solar systems to inverters with active cooling
In photovoltaic and wind power systems, electronic components such as inverters and power converters are of central importance as they convert the generated energy into usable electricity. These components can generate a considerable amount of heat and require effective cooling systems to ensure optimal operating temperatures and a long service life.
At the same time, these electronic components are exposed to the prevailing influences such as heat, cold, storms, dust and moisture when used outdoors. Renewable energy systems are therefore faced with the challenge of defying extreme weather conditions while still reliably supplying electricity. Electronic systems in wind turbines or solar parks should require as little maintenance as possible due to their difficult accessibility. The demands on the cooling systems used are therefore high: for use on wind turbines or solar modules, they should not only be corrosion-resistant, but also offer long-lasting reliability and minimise maintenance requirements.
At the same time, these electronic components are exposed to the prevailing influences such as heat, cold, storms, dust and moisture when used outdoors. Renewable energy systems are therefore faced with the challenge of defying extreme weather conditions while still reliably supplying electricity. Electronic systems in wind turbines or solar parks should require as little maintenance as possible due to their difficult accessibility. The demands on the cooling systems used are therefore high: for use on wind turbines or solar modules, they should not only be corrosion-resistant, but also offer long-lasting reliability and minimise maintenance requirements.
Increased efficiency for renewable energies: Innovative cooling technologies for photovoltaic and wind power systems
Passive high-performance heat sinks, which dissipate heat from the DC/DC converter through free convection and radiation, are therefore the first choice for use in photovoltaic and wind power systems. The large housing surfaces are also ideal for dual use as heat sinks, manufactured using the extrusion process with CNC post-processing or as die-cast aluminium.
In more protected areas, where power electronics also generate a lot of heat loss, various active cooling systems are available. They can be designed in particular for buffering thermal load peaks. Forced ventilation, for example via a fan, is therefore not necessary in continuous operation, which reduces the wear and maintenance requirements of these fans.
In more protected areas, where power electronics also generate a lot of heat loss, various active cooling systems are available. They can be designed in particular for buffering thermal load peaks. Forced ventilation, for example via a fan, is therefore not necessary in continuous operation, which reduces the wear and maintenance requirements of these fans.
Your heat sink manufacturer for photovoltaic and wind power electronics
EKL specialises in the development and construction of electronic applications for renewable energies. We will find a customised and cost-optimised cooling solution for you to ensure the performance and reliability of your systems in a wide range of applications.
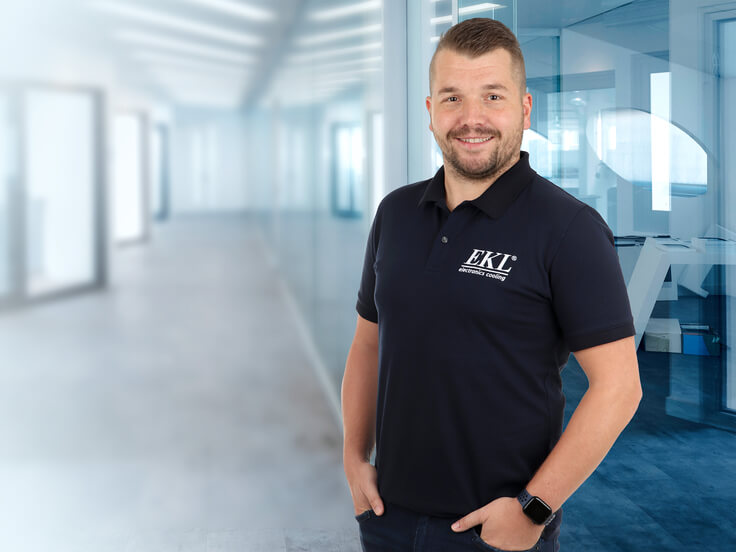
Let's talk about your cooling task!
Raphael Kroll
Sales Department
+49 (0)7561 9837-27
r.kroll@ekl-ag.de
Make an appointment Enquiries by e-mail
Raphael Kroll
Sales Department
+49 (0)7561 9837-27
r.kroll@ekl-ag.de
Make an appointment Enquiries by e-mail
Electronic components for wind power plants with high cooling requirements
In electronics, the heat generated by current-carrying components is an unavoidable and usually annoying side effect. As a product manager and development engineer of electronic systems, free yourself from the risk of overheating and expensive development loops by placing the thermal management of your device in the hands of EKL! We see ourselves as a partner in your development, pursuing the same goals as you: to manufacture a reliable, high-quality and durable product at competitive prices.
Cooling control units in wind turbines
The control electronics in wind turbines perform essential tasks such as operational management, safety monitoring, control and operating data acquisition. It is responsible for optimising the energy yield by tracking the rotor blades to the wind direction and regulating the output by adjusting the blades. It is responsible for ensuring that the wind turbine is in a safe operating state, especially during storms. The components to be cooled primarily include the inverters, the control units and the generators. They all generate heat loss, which must be efficiently dissipated using heat sinks.
Cooling wind turbine inverters and transformers
The DC voltage generated by the rotation of the blades in the generator is converted into AC voltage by the power electronics in the inverter. The transformed high voltage is fed into the power grid. This conversion is necessary for the transport of renewable energy to the consumer. The components in wind turbines that need to be cooled include the inverters themselves, which produce power losses in the form of heat. The transformers, which convert the generator voltage to 10,000 - 30,000 volts, also require effective cooling systems to maintain their functionality.
Cooling power electronics in wind turbines
The power modules (MOSFET, IGBT, power transistors) installed in the control units and inverters switch and regulate high currents. The heat loss generated by these components is correspondingly high and must be dissipated quickly.
Cooling communication electronics
The communication electronics in wind turbines perform essential tasks such as monitoring the system status, collecting statistical operating data and controlling switches as well as communicating with the operator. It is responsible for the data connections for sending alarms or requesting maintenance services.
Cooling sensors and measuring devices in wind turbines
Important data such as wind speed, wind direction, rotor blade position and the position of the nacelle to optimise the alignment and performance of the wind turbines are recorded by robust sensors and measuring devices. If they fail due to overheating or provide incorrect information, the turbine will run inefficiently or even stops. Effective cooling systems are therefore essential to prevent the electronic components from overheating and to ensure the operational safety of the wind turbine.
Electronic components for private and commercial solar systems with high cooling requirements
The task of solving heat problems in the electronic components of your solar systems is in good hands with our experts at EKL. Our cooling professionals have specialised knowledge and experience in heat dissipation and cooling. Working with EKL as a specialised partner significantly shortens your development time and contributes to a faster market launch. We enable your product managers and developers to concentrate on their core competences. At the same time, we ensure that critical components are handled professionally, for example:
Cooling inverters for PV systems
Inverters in solar power systems have the task of converting the direct current (DC) generated by the solar modules into alternating current (AC), which can then be fed into the public grid or used for domestic purposes. They are therefore a central element of every solar system. The components to be cooled include the power electronics in the inverter, which also emit a lot of heat loss due to the high currents.
Cooling DC/DC converters in photovoltaic systems
DC/DC converters can convert higher voltages into lower voltages or vice versa, which is important for the efficiency of the PV system. Well-dimensioned heat sinks ensure that the heat is effectively dissipated from the sensitive components.
Cooling charge controllers for battery storage of solar energy
Charge controllers in solar systems have the task of controlling and optimising the charging process of the battery storage system. They protect the battery from overcharging and deep discharging, which extends its service life. Various components such as power transistors and thyristors require heat sinks to prevent overheating and maintain the efficiency of battery storage.
Smart Home Mini Server for optimum solar energy utilisation cooling
The best possible use of solar power is achieved by intelligently controlling energy production, the charging and discharging of the battery storage system, the charging station for electric cars and other smart energy devices as required. Smart Home Servers optimise the self-consumption of solar power through intelligent energy management, resulting in more efficient use. The components that need to be cooled usually include the inverters and battery storage systems. When converting and storing electricity, these components generate heat losses.
Cooling battery management systems for electricity storage
Battery management systems (BMS) in photovoltaic systems perform important tasks such as protecting the battery cells from overcharging and deep discharge, monitoring and controlling the voltage, temperature, capacity and state of charge of the batteries and equalising the state of charge of individual cells. All of this contributes to optimising the performance and extending the service life of the solar power storage system.
High-performance heat sinks for wind power and solar energy
EKL - Everything from a single source
The temperature of electronic components must remain within the tolerated range, as excessive heating can shorten their service life and impair their performance. EKL provides you with expert support in solving these heat problems efficiently and economically using passive heat sinks, fans, heat pipes, liquid heat sinks or other thermal management technologies.
EKL is therefore your perfect solution partner for cost-optimised temperature regulation of all components in your electronic device. We are at your side in every project phase, from the initial idea, design and prototype construction through to series production - and beyond!
The temperature of electronic components must remain within the tolerated range, as excessive heating can shorten their service life and impair their performance. EKL provides you with expert support in solving these heat problems efficiently and economically using passive heat sinks, fans, heat pipes, liquid heat sinks or other thermal management technologies.
EKL is therefore your perfect solution partner for cost-optimised temperature regulation of all components in your electronic device. We are at your side in every project phase, from the initial idea, design and prototype construction through to series production - and beyond!
Personal point of contact
From the initial project phase to the delivery of your customised cooling technology, you will always have a personal point of contact at EKL We are always available to provide you with competent and responsive support.
Full service from the idea to logistics
Concentrate your core competence on product development. We offer all project services relating to cooling - from the initial consultation, idea development and thermal simulation, prototype construction and optimisation, through to punctual delivery and reliable logistics and warehousing.
Variety of manufacturing technologies
We are one of the heat sink manufacturers with the widest range of manufacturing technologies. This enables us to offer a service portfolio that is designed for the development and production of your truly best cooling solution - at an excellent price-performance ratio.
Performance optimisation + cost optimisation
EKL actively supports you in reducing your manufacturing costs without compromising quality or performance. Product cost reduction is an important aspect that we achieve for you through efficient design, careful material selection and reliable manufacturing partners.
Pre-assembled assemblies + packaging
We actively assist your production staff by supplying pre-assembled assemblies. This not only reduces your labour costs per device, but also guarantees the highest quality. Your sensitive heat sinks or assemblies are protected for transport using customised packaging.
Warehouse and logistics in Germany
With over 1100 pallet spaces, we offer tailor-made logistics solutions and minimise your storage costs through stockpiling and consignment stock, just-in-time deliveries, coordinated delivery schedules and flexible shipping options for individual requirements.
The EKL project stages for your cooling solutionChoose your point of entry!
Our offer is as flexible as your needs. Are you still early in the development phase and want an idea generator for the best cooling solution? Do you have a ready-made device that gets too hot? Or are you simply looking for an alternative or additional supplier for a heat sink already used in series production? In EKL you will always find a flexible, agile and responsible partner for the cooling of your electronic components and complete systems, whatever the project phase. We look forward to your enquiry!
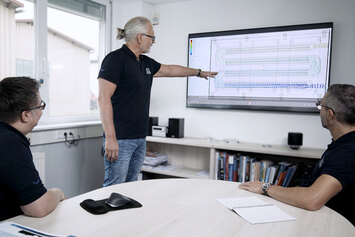
Counselling
Concept
Concept
In personal contact and open dialogue with you, our engineers create the creative space and framework to design the best cooling solution for your requirements from the wealth of options available.
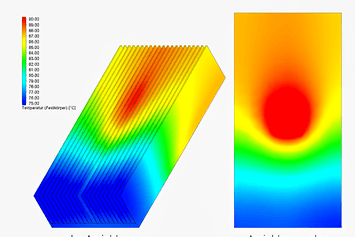
Development
Feasibility / simulation
Feasibility / simulation
We test the idea for your heat sink virtually in the thermal simulation. Realistic computer simulations allow variations in manufacturing processes, system structures and other parameters.

Performance optimisation
Even a well-functioning heat sink can still be optimised. We determine the "how" and "how much" by simulating different materials or cooling technologies, for example, as well as simulating various environmental parameters.
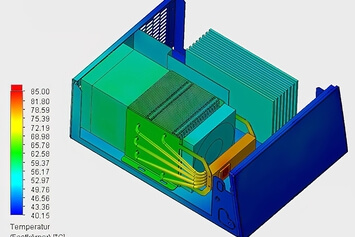
Cost optimisation
An expensive heat sink can often be made significantly cheaper by using an alternative manufacturing process. Whether with the same or application-specific performance: we support your product development in reducing costs.
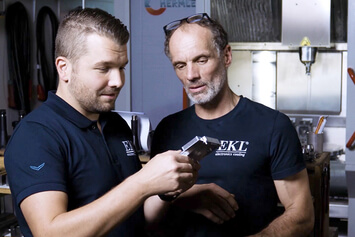
Production drawing
Prototype construction
Prototype construction
Prototypes from our design department enable early testing and targeted solutions to problems in your device. We create your functional and design prototypes with our in-house CNC production.
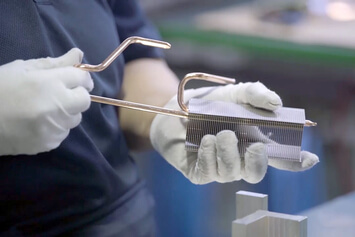
Series production
small to large
small to large
By manufacturing in-house and in Asia, we can offer all types of heat sinks from small to large series at competitive unit prices. We impress our long-standing customers with our consistently high quality.
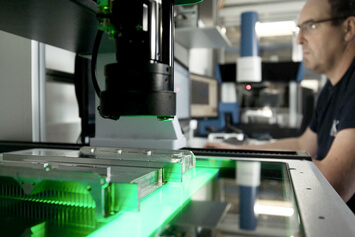
Sampling
Incoming goods inspection
Incoming goods inspection
We make no compromises when it comes to quality: Development takes place in Germany and all series products are analysed by our German test laboratory according to test plans using state-of-the-art methods.
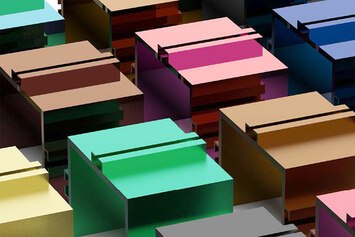
Surface finishing
Anodising, powder coating, painting etc. protect your heat sinks from corrosion and environmental influences. But colour is not just chic, because dark-coloured heat sinks also emit more radiant heat.
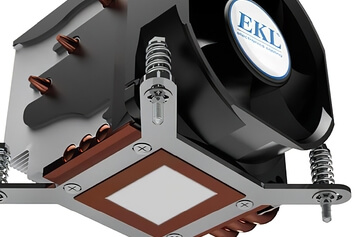
Assemblies
Pre-assembly
Pre-assembly
We actively relieve your production with pre-assembled assemblies. This reduces your workload per device and guarantees the highest quality, because as cooling professionals we ensure that the heat sink is optimally attached.
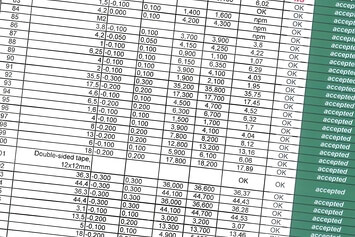
Quality assurance
Test plans
Test plans
We test according to our own and customer-specific test plans using the latest rapid thermal measuring equipment, 3D measuring machines, assembly tests and testing of various application scenarios.
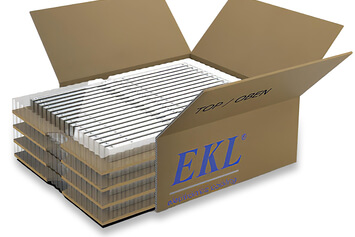
Packaging design
Packaging production
Packaging production
EKL develops and produces customised packaging to optimally protect your sensitive heat sinks or assemblies in the sometimes harsh transport and storage environments.
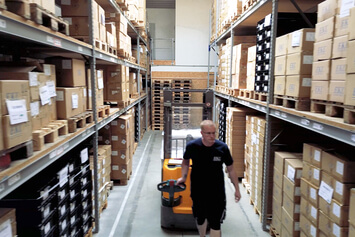
Warehouse
& Logistics
& Logistics
With large storage capacities, we offer production-related stocking and consignment warehouses, just-in-time deliveries, customised delivery schedules and flexible shipping options for your individual requirements.
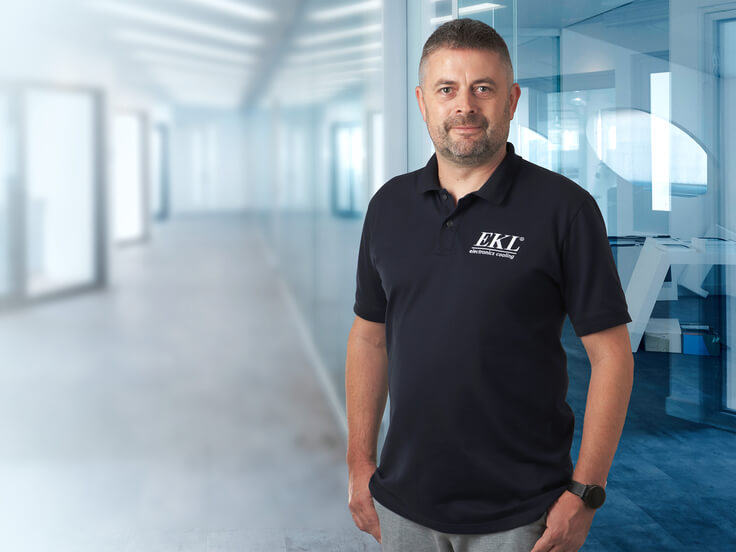
Let's talk about your cooling task!
Frank Sichler
Sales Manager
+49 (0)7561 9837-47
f.sichler@ekl-ag.de
Make an appointment Enquiries by e-mail
Frank Sichler
Sales Manager
+49 (0)7561 9837-47
f.sichler@ekl-ag.de
Make an appointment Enquiries by e-mail