Cold forging pin fin heat sinks using the cold extrusion process
Pin fin heat sinks pressed from aluminium or copper in a single work process
In this technology, also known as cold forming, a piece of high-purity aluminium or copper (depending on the cooling concept) is pressed into the mould at normal room temperature under high pressure. As a result, the metal - similar to plastic injection moulding - completely fills the mould of the pin heat sink with all its fine structures. Although the forming energy heats the metal slightly, the temperature change is too small to affect the dimensional accuracy of the moulded part.
Advantages of cold forging
- Copper heat sink and aluminium heat sink "in one piece"
- High-purity aluminium or copper with very good thermal conductivity
- High material compaction further improves thermal conductivity
- Tight dimensional tolerances achievable
- Large surface area possible thanks to round pins
- Increased strength and robustness
- Standard sizes and shapes available
- Various surface finishes possible
(anodising, chromating, painting, powder coating, etc.)
A heat sink emerges from the moulding press that hardly requires any reworking despite its complex geometry. The most commonly used pin shape is cylindrical ("pin fin"), as it forms large surfaces for heat dissipation with excellent air circulation. Customised pin coolers and designs can therefore be implemented very easily.
Increased performance of pin fin heat sinks by combining different techniques
Due to their extremely homogeneous and dense material structure, heat sinks made using the cold extrusion process offer excellent thermal conductivity, which is often higher than that of the base material. This property can be further optimised by combining it with other cooling technologies. The high dimensional accuracy and surface quality, as well as the high degree of design freedom, allow precise adaptation to complementary fan or liquid-based cooling technologies.
Pin Fin heat sink+ fan
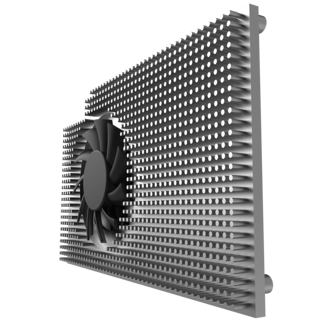
The combination of pin fin heat sinks with forced ventilation accelerates heat dissipation and therefore offers higher cooling performance. They also work effectively in environments with little or no natural convection. The use of a fan allows increased fin density for improved heat transfer. The smaller installation space required and the smaller size compared to systems with free convection allow a more compact design. EKL offers a wide range of its own fan models as well as fans from well-known brands such as ebm-papst, SANYO DENKI, ADDA, JAMICON, STK and Everflow.
Pin Fin heat sink+ plastic air duct
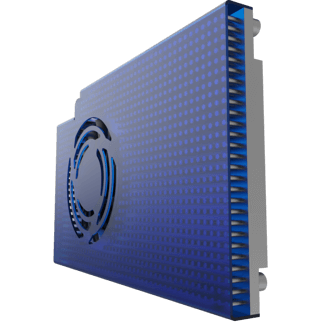
The efficiency of heat dissipation can be increased through a targeted air flow, which is particularly important in compact systems. In addition, the chimney effect is enhanced by the ventilation duct, which improves passive cooling through natural convection and thus supports efficient heat dissipation even without active ventilation components.
Pin Fin heat sink+ heatpipes
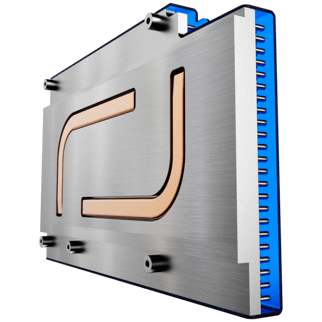
The faster heat spread through heat pipes distributes the heat efficiently across the heat sink, which enables even heat distribution. This helps to avoid hotspots and transport the heat to more distant locations, which is particularly important in compact systems. In addition, this technology enables weight savings without compromising cooling performance.
Pin Fin heat sink+ vapour chamber
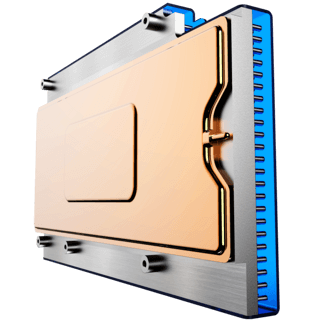
The operating principle of the vapour chamber accelerates the heat spread and the heat is efficiently dissipated from the source to the pin fins. The pin fins ensure an even distribution of heat over a large surface area and avoid hotspots. The vapour chamber is significantly lighter than a solid copper plate. In addition, the low temperature gradient prevents excessive thermal stress on the components, which increases service life and reliability.
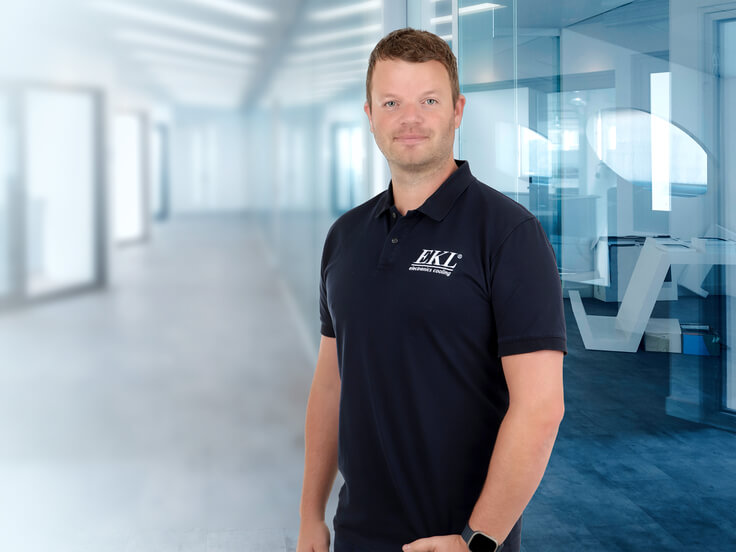
Let's talk about your cooling task!
Thomas Würzer
Sales Department
+49 (0)7561 9837-44
t.wuerzer@ekl-ag.de
Make an appointment Enquiries by e-mail
Thomas Würzer
Sales Department
+49 (0)7561 9837-44
t.wuerzer@ekl-ag.de
Make an appointment Enquiries by e-mail
Pin Fin Cooling for high heat dissipation and cooling performance
Pin heat sinks are an efficient solution for heat dissipation in electronic components, especially in power electronics, where space and weight are often limited. They are ideally suited as pin fin heat sinks for components with high power dissipation, such as IGBTs (Insulated Gate Bipolar Transistors), output stages, MOSFETs (Metal-Oxide-Semiconductor Field-Effect Transistors), as high-performance LED heat sinks and for similar components.
Thanks to their design, pin heat sinks enable rapid heat spreading and effective heat dissipation, even in compact spaces. The high material density and high thermal conductivity of the pure aluminium alloys or copper alloys help to ensure that the heat is conducted quickly from the base plate to the tips of the pins. This is particularly advantageous in conjunction with forced convection, i.e. when a fan supports heat dissipation.
Thanks to their design, pin heat sinks enable rapid heat spreading and effective heat dissipation, even in compact spaces. The high material density and high thermal conductivity of the pure aluminium alloys or copper alloys help to ensure that the heat is conducted quickly from the base plate to the tips of the pins. This is particularly advantageous in conjunction with forced convection, i.e. when a fan supports heat dissipation.
Added value and extras
Our full service goes beyond the mere development, series production and logistics of your heat sinks. Do you need special bores or milling on your heat sinks? Do you want your heat sink to not only dissipate a lot of heat, but also look stylish? Would you like a product ready-to-plug-in with all accessories?
Welcome to EKL!
Welcome to EKL!
CNC machining
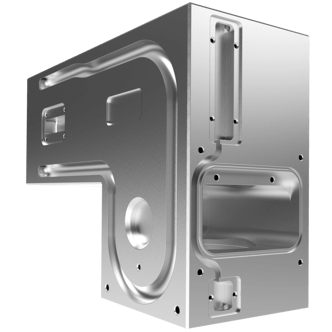
For prototypes, small series and customised reworking of heat sinks, we have modern 3- and 5-axis CNC milling machinesat our company headquarters. Complex machined and high-precision radiators are our speciality. Working areas of the machines:
Hermle C 400 (5-axis) 850 x 700 x 500 mm | Mikron VCE1000pro (3-axis) 1000 x 560 x 600 mm | Kondia B1050 (3-axis): 1000 x 500 x 600 mm
Hermle C 400 (5-axis) 850 x 700 x 500 mm | Mikron VCE1000pro (3-axis) 1000 x 560 x 600 mm | Kondia B1050 (3-axis): 1000 x 500 x 600 mm
Surface finishing
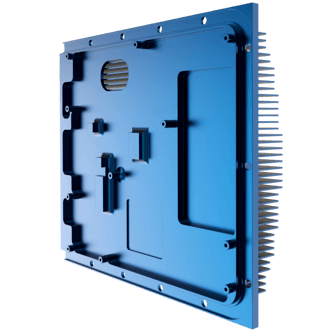
Our range includes various surface finishes to create a durable, corrosion-resistant surface. Nickel plating increases wear resistance and lustre. Chromating and passivation, especially with Surtec 650, provide additional protection against corrosion. Powder coating is another option for a robust and durable coloured surface. Painting and cathodic dip coating round off our wide range of surface colours and textures.
Attachments & accessories
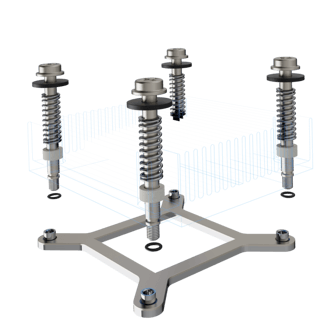
Depending on the application, screws, springs or push pins ensure the secure and stable attachment of the heat sinks. Backplates provide additional stability and improved heat dissipation. Heat-conducting pastes and pads are naturally part of our range to enable optimum heat transfer between the heat sink and the heat source.
Secure packaging for transport
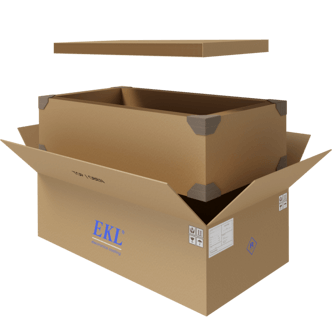
With a focus on perfect protection during transport, we develop packaging that not only fits perfectly but is also robust. Another important aspect of the range is the use of recyclable materials that contribute to sustainability and environmental friendliness.
Cold forged heat sinks in typical application areas
Cold forged heat sinks, manufactured from aluminium or copper, are popular in many areas of application due to their high thermal conductivity. These materials allow heat to be transferred quickly from the source to the heat sink. Aluminium in particular offers a good ratio between thermal conductivity and cost, while copper is even more efficient but also more expensive. The variety of shapes achieved through cold forging enables customisation to specific cooling requirements for a wide range of applications.
The EKL project stages for your cooling solutionChoose your point of entry!
Our offer is as flexible as your needs. Are you still early in the development phase and want an idea generator for the best cooling solution? Do you have a ready-made device that gets too hot? Or are you simply looking for an alternative or additional supplier for a heat sink already used in series production? In EKL you will always find a flexible, agile and responsible partner for the cooling of your electronic components and complete systems, whatever the project phase. We look forward to your enquiry!
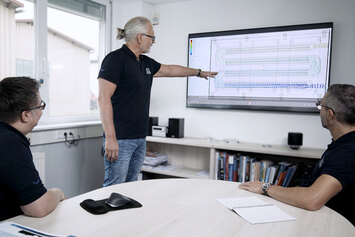
Counselling
Concept
Concept
In personal contact and open dialogue with you, our engineers create the creative space and framework to design the best cooling solution for your requirements from the wealth of options available.
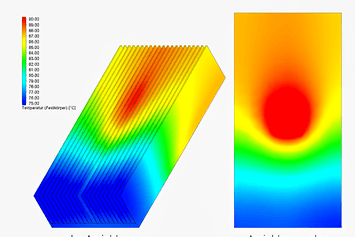
Development
Feasibility / simulation
Feasibility / simulation
We test the idea for your heat sink virtually in the thermal simulation. Realistic computer simulations allow variations in manufacturing processes, system structures and other parameters.

Performance optimisation
Even a well-functioning heat sink can still be optimised. We determine the "how" and "how much" by simulating different materials or cooling technologies, for example, as well as simulating various environmental parameters.
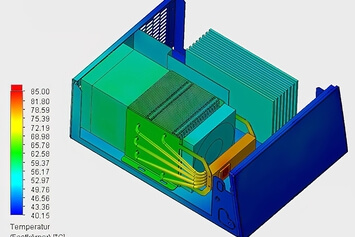
Cost optimisation
An expensive heat sink can often be made significantly cheaper by using an alternative manufacturing process. Whether with the same or application-specific performance: we support your product development in reducing costs.
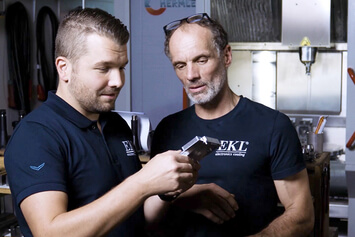
Production drawing
Prototype construction
Prototype construction
Prototypes from our design department enable early testing and targeted solutions to problems in your device. We create your functional and design prototypes with our in-house CNC production.
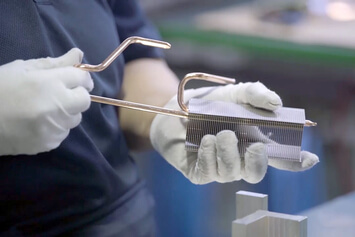
Series production
small to large
small to large
By manufacturing in-house and in Asia, we can offer all types of heat sinks from small to large series at competitive unit prices. We impress our long-standing customers with our consistently high quality.
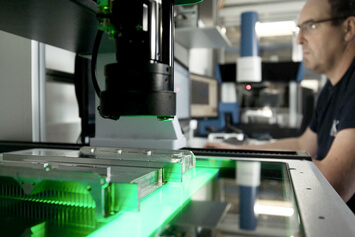
Sampling
Incoming goods inspection
Incoming goods inspection
We make no compromises when it comes to quality: Development takes place in Germany and all series products are analysed by our German test laboratory according to test plans using state-of-the-art methods.
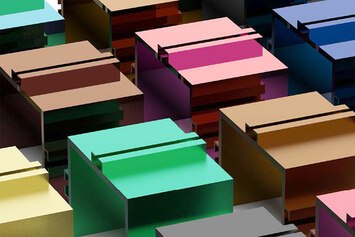
Surface finishing
Anodising, powder coating, painting etc. protect your heat sinks from corrosion and environmental influences. But colour is not just chic, because dark-coloured heat sinks also emit more radiant heat.
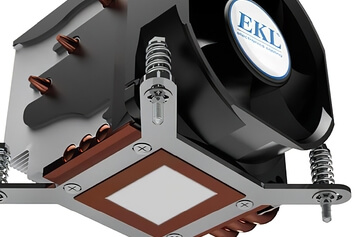
Assemblies
Pre-assembly
Pre-assembly
We actively relieve your production with pre-assembled assemblies. This reduces your workload per device and guarantees the highest quality, because as cooling professionals we ensure that the heat sink is optimally attached.
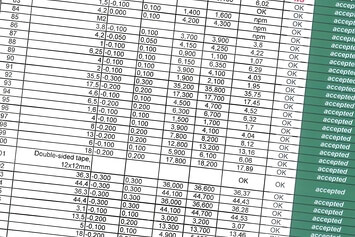
Quality assurance
Test plans
Test plans
We test according to our own and customer-specific test plans using the latest rapid thermal measuring equipment, 3D measuring machines, assembly tests and testing of various application scenarios.
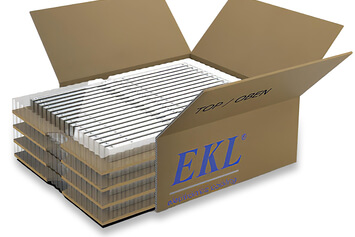
Packaging design
Packaging production
Packaging production
EKL develops and produces customised packaging to optimally protect your sensitive heat sinks or assemblies in the sometimes harsh transport and storage environments.
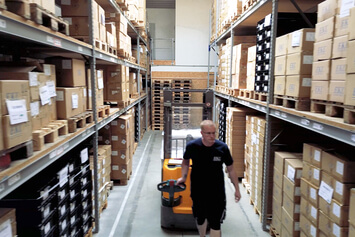
Warehouse
& Logistics
& Logistics
With large storage capacities, we offer production-related stocking and consignment warehouses, just-in-time deliveries, customised delivery schedules and flexible shipping options for your individual requirements.
Direct comparison of cold forging manufacturing processes
A filter is active, some data is hidden
• less suitable | ••••• excellently suited | n.a.: not applicable
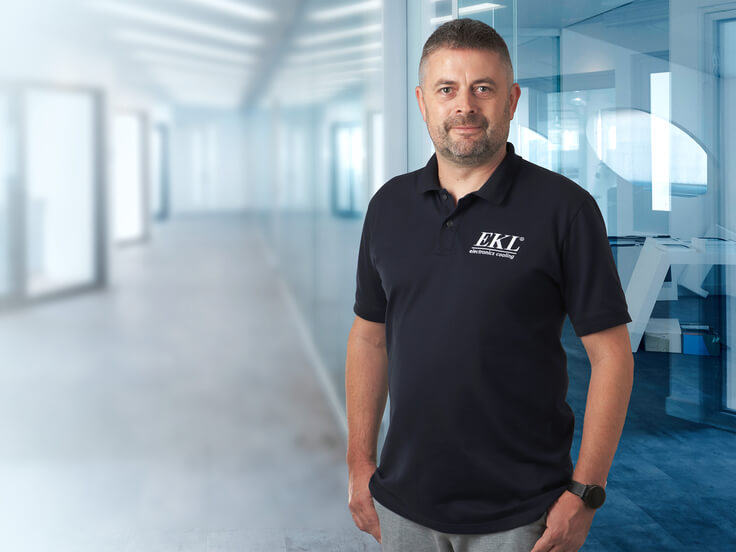
Let's talk about your cooling task!
Frank Sichler
Sales Manager
+49 (0)7561 9837-47
f.sichler@ekl-ag.de
Make an appointment Enquiries by e-mail
Frank Sichler
Sales Manager
+49 (0)7561 9837-47
f.sichler@ekl-ag.de
Make an appointment Enquiries by e-mail